Model C
general description
Model C series is the advanced choice for large-scale production. Its efficient condensing system and advanced emission control system combine to offer excellent performance, setting new standards in efficiency and environmental responsibility.
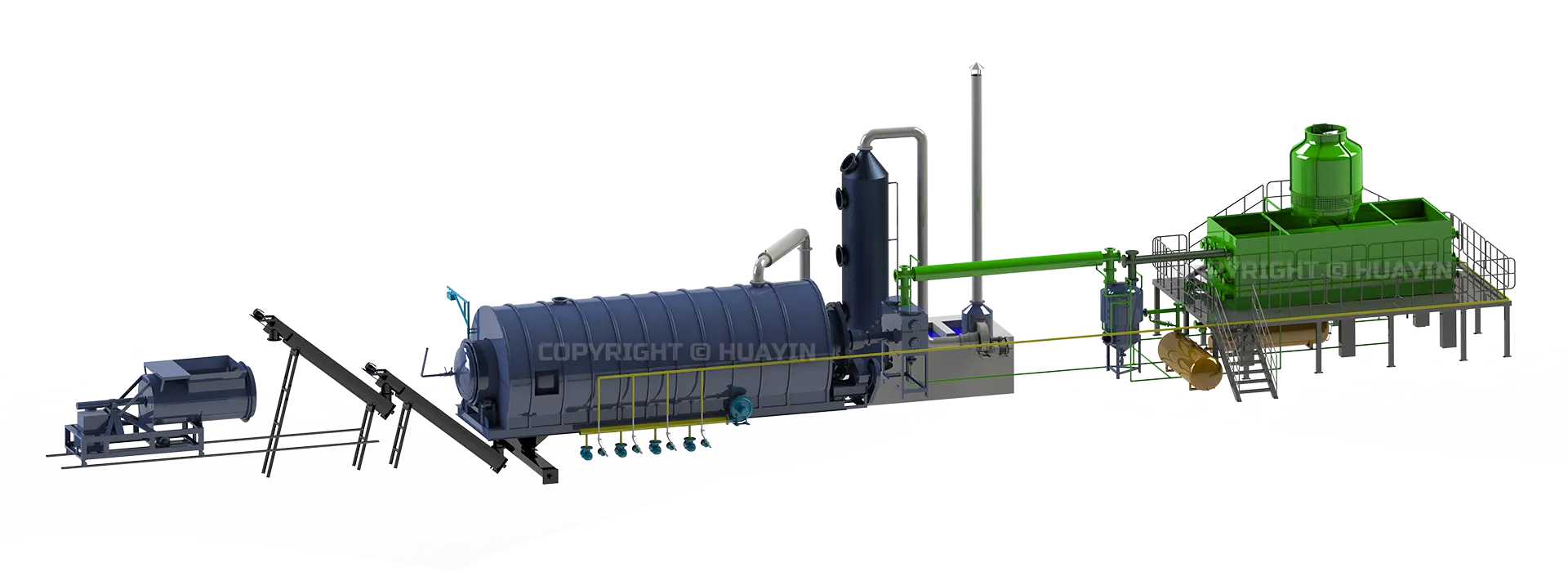
The reactor is the main vessel where the thermal decomposition of raw materials takes place. It is a high-temperature chamber designed to operate in the absence of oxygen, creating a controlled environment for the pyrolysis process.
After the pyrolysis process, the gases and vapors produced need to be cooled and condensed to convert them into liquid form. The condensation system typically consists of a series of heat exchangers or condensers that utilize cooling mediums like water or air to extract heat from the gases and vapors. This condensation process allows for the collection of liquid products, such as fuel oil.
The solid residue or char left after the pyrolysis process, commonly referred to as carbon black, needs to be collected and managed. The plant may include mechanisms for its extraction, such as screw conveyors, to transport the carbon black to storage or further processing facilities.
It’s responsible for cleaning and purifying the exhaust gases generated during pyrolysis. It includes scrubbers and filters to remove impurities, particulate matter, and potentially harmful emissions from the gas stream. This system helps to comply with environmental regulations and ensures the safe operation of the pyrolysis plant.
Item | Value |
---|---|
Unit Capacity | 5~15 Tons |
Production Mode | Batch Type |
Overall Dimension | 35m x 12m x 8m (LxWxH) |
Total Weight | 35~50 Tons |
Condensing System | Square Box Condenser |
Emission Control System | Stainless Steel Scrubber plus Internal Filters |
Heating System | Oil Burners & Gas Burners |
Feeding System | Hydraulic Feeder |
Discharging System | U-shape Screw Conveyor |